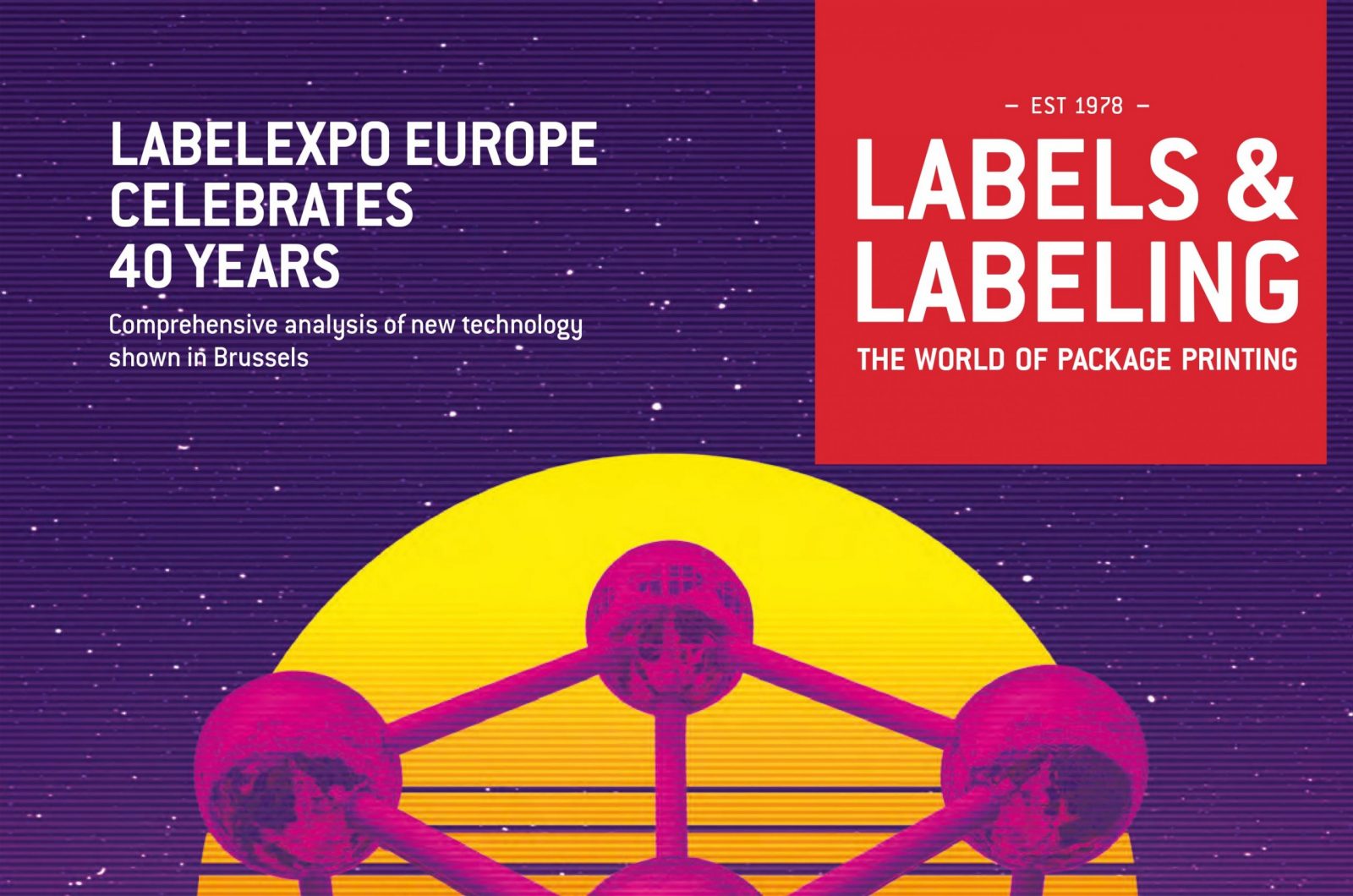
Quality control at the digital pre-press stage
According to All4Labels, its site in Trittau, Germany, has developed over the last three years into the world’s largest print center for adhesive labels.
As such, given the volume of orders received and frequent changeovers, optimization of production processes has become All4Labels’ main priority. Last year, the company integrated its pre-press inspection – provided by EyeC – into its Esko workflow, resulting in increased efficiency and reliability.
All4Labels installed EyeC’s Proofiler 600DT in Trittau in 2016 for automated print sample inspection of pharmaceutical labels, alongside workflow software from Esko. Following the successful automation of the production process, the company turned its focus to its pre-press processes, integrating them in 2018 into its existing workflow using EyeC Workflow Integration.
Automated incoming data checks
In recent years, requirements across all industry sectors, in particular for pharma products, have increased across the production chain. Before the workflow integration, the incoming data inspection at All4Labels was largely completed manually. With the help of a soft proof, the customer data was standardized in the pre-press stage and approved by the customer before printing.
The unique challenge here came in dealing with print data without a prior approval process. In addition to the risk of changes, such as shifts or missing design elements, manual inspecting
was also time- and resource-consuming. Production processes
that were already automated were also slowed down by manual pre-press inspections. Along with increased productivity, automated inspection of texts, graphics and 1D as well as 2D codes with the EyeC Proofiler Graphic now provides additional reliability within the incoming data controls.
The configuration of artwork inspection was completed in cooperation with EyeC so that inspection is now possible across almost all jobs. In comparison, the inspection of print data with high customer requirements, such as pharma labels, is carried out with different inspection parameters. Based on the respective customer number, the parameters are automatically selected
so that inspection is carried out in the workflow according to customer requirements and without manual steps. Today, the right configuration of the inspection profiles ensures the consistent quality of all delivered print jobs and gives those responsible more security in the preparation and execution of print jobs throughout the pre-press and production stages.
‘Among other things, we decided on EyeC because, from the beginning, it was clearly communicated what the system could provide us. Together with EyeC, we configured the variety of setting possibilities for the inspections to meet our specific requirements. Furthermore, there are additional options available such as Braille inspection, which we can profit from in the nearer future,’ said Michael Koch, head of pre-press digital printing at All4Labels.
Fully-automated Inspection of 2D Codes
In addition, the step-and-repeat files from two major customers are automatically inspected with the help of the EyeC Workflow Integration at All4Labels in Trittau. Therefore, the EyeC Proofiler Graphic is used for the inspection of 2D codes. For this, the QR code provided by the customer is entered into the MIS through the Account Manager in the first step. After the print job has been created, the Proofiler Graphic inspects the codes in the pre-press stage against stored data. In addition to the readability check, the system inspects the information contained in the codes, such as the article number so that variety mix-ups are excluded.
The pre-press inspection of personalized pharma labels continues to present a challenge. Because the required evaluations in the workflow are both time- and resource-consuming, an adaptation of operational processes and the appropriate configuration of inspection parameters are required.
‘Especially in the pharmaceutical sector, we see great potential in digital printing with variable data and therefore have already set up a closed-loop system in our workflow,’ says Koch. ‘In the future, the multi-page PDF provided by the customer is loaded directly on the press and will automatically be inspected. Print defects are automatically detected and marked or reprinting is directly initiated. In addition, the final report contains all information for the automatic replacement of defective labels and serves as proof to the customers. With EyeC’s system, we are already prepared for future challenges today.’
All4Labels
All4Labels has more than 3,000 employees at 29 locations worldwide. The site in Trittau employs almost 200 people, including more than 105 experts in the digital printing sector.